Master the Basics of Standard Costing with This Simple Step-by-Step Guide
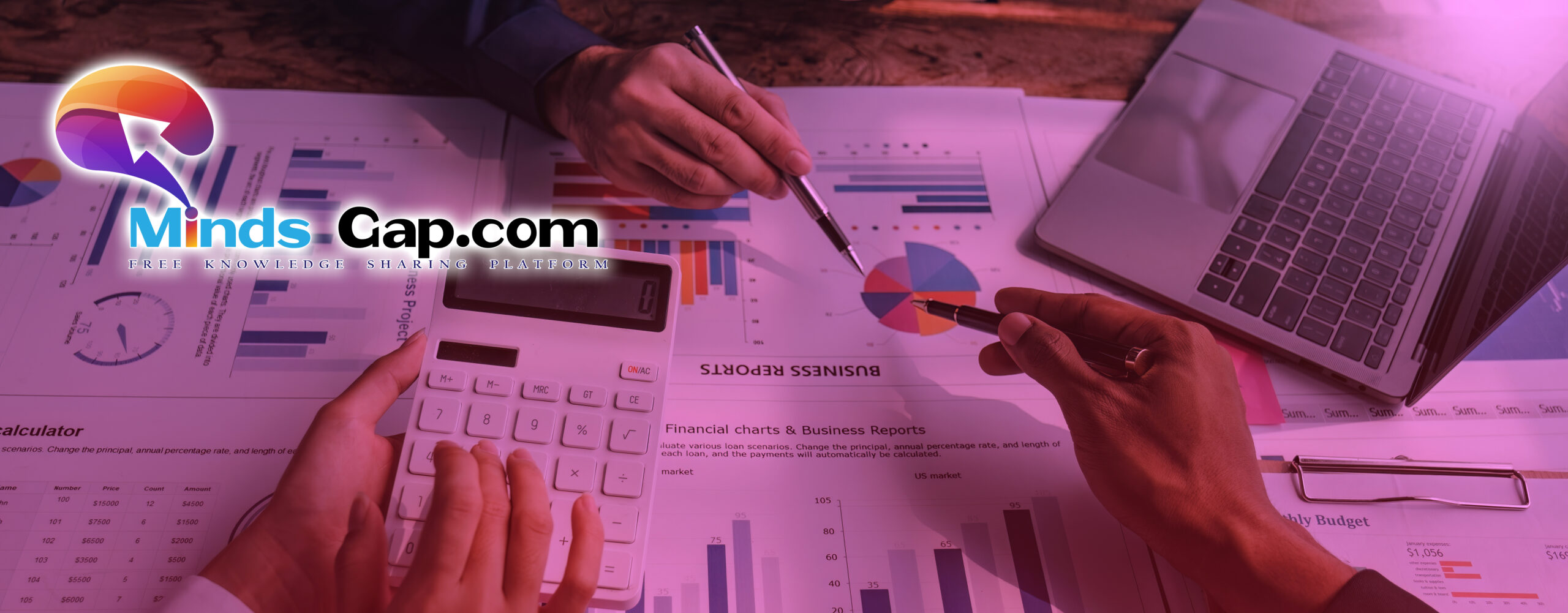
This guide provides a clear and accessible guide to standard costing, breaking down complex concepts into manageable steps. It covers establishing standard costs for materials, labour, and overheads, calculating variances, and interpreting results. The guide aims to provide a solid foundation for those seeking proficiency in cost accounting, enabling them to grasp key principles and gain practical insights for their organization. It empowers individuals with the knowledge needed to excel in today’s competitive business landscape.
What is Standard Costing?
Standard costing is a management accounting technique where predetermined costs are established for various elements involved in the production of goods or services. These predetermined costs, known as standards, serve as benchmarks against which actual costs are compared. By analysing the variances between actual and standard costs, businesses can assess their operational performance, control costs, and make informed decisions to improve efficiency and profitability.
Purpose:
- Cost Control
Standard costing helps in controlling costs by providing a predetermined benchmark against which actual costs can be compared. This enables businesses to identify and address areas of inefficiency or excess spending.
- Performance Evaluation
It allows for the evaluation of operational performance by comparing actual costs to standard costs. Variances between the two provide insights into how efficiently resources are being utilised.
- Decision Making
standard costing provides reliable cost information for making informed decisions regarding pricing, production planning, budgeting, and resource allocation.
- Budgeting
It facilitates the process of budgeting by providing predetermined cost standards that serve as a basis for setting financial targets and allocating resources effectively.
Benefits:
- Cost Reduction
By identifying and addressing variances between actual and standard costs, businesses can implement corrective actions to reduce costs and improve profitability.
- Efficiency Improvement
Standard costing promotes efficiency improvement by highlighting areas where resources are being underutilised or wasted, allowing for adjustments to enhance productivity.
- Performance Monitoring
It enables businesses to monitor their performance against predetermined targets and take timely corrective actions to stay on track towards achieving their goals.
- Enhanced Decision-Making
Businesses can make better decisions regarding pricing strategies, product mix, investment opportunities, and resource allocation with the accurate cost information that standard costing provides.
- Benchmarking
Standard costing provides a benchmark for comparing performance across different departments, products, or periods, enabling businesses to identify best practices and areas for improvement.
- Financial Reporting
It facilitates the preparation of financial reports by providing standardised cost information that can be easily compared across different periods or business units.
Components of Standard Costing
By establishing following components, businesses can create a comprehensive framework for cost estimation, performance evaluation, and decision-making within their operations.
The components of standard pricing typically include:
- Standard Direct Materials Cost
This represents the predetermined cost per unit of direct materials required for production. It includes the standard price per unit of material and the standard quantity of material per unit of output.
- Standard Direct Labour Cost
This comprises the predetermined cost per unit of direct labour needed for production. It involves the standard labour rate per hour and the standard hours of labour required per unit of output.
- Standard Manufacturing Overhead Cost
This encompasses the predetermined overhead cost per unit of output. It incorporates various indirect manufacturing costs such as factory rent, utilities, depreciation, and maintenance, allocated based on a standard overhead rate.
- Standard Variable Costs
These are costs that vary in direct proportion to changes in production volume or activity level. They include standard direct material and direct labour costs.
- Standard Fixed Costs
These are costs that remain constant regardless of changes in production volume or activity level. While not always explicitly included in standard costing, they are important to consider for comprehensive cost analysis.
- Standard Total Cost
This represents the sum of standard direct materials, direct labour, and overhead costs per unit of output. It provides the overall standard cost per unit of production.
Setting Standard Costs
Setting standard costs involves establishing predetermined benchmarks for various cost components involved in the production of goods or services. These benchmarks serve as targets or expectations against which actual costs are compared. Setting standard costs typically involves analysing historical data, industry benchmarks, and future expectations to determine the standard cost for items such as direct materials, direct labour, and manufacturing overhead. These standards provide a basis for cost control, performance evaluation, and decision-making within an organization. By setting standard costs, businesses can more effectively manage their resources, identify areas for improvement, and strive for operational efficiency and profitability.
Calculating Variances
Standard costing requires the comparison of actual costs with predetermined standard costs to calculate variances. The key variances can be determined through this process.
Material Price Variance
Material price variance is a crucial factor in standard costing, revealing the difference between actual and standard costs of raw materials. It helps businesses identify inefficiencies and take corrective actions. It can reveal cost-saving opportunities and help make decisions about suppliers and pricing agreements because of market fluctuations, supplier negotiations, and material quality. Thus, it is a key performance indicator.
Material Price Variance
Material price variance is a crucial factor in standard costing, revealing the difference between actual and standard costs of raw materials. It helps businesses identify inefficiencies and take corrective actions. It can reveal cost-saving opportunities and help make decisions about suppliers and pricing agreements because of market fluctuations, supplier negotiations, and material quality. Thus, it is a key performance indicator.
Formula:
Material Price Variance = (Actual Quantity × Actual Price) – (Actual Quantity × Standard Price)
Material Usage Variance
Material usage variance is a crucial factor in standard costing, indicating the difference between actual and standard material usage. It can indicate waste or inefficiency in production processes and potential issues within the supply chain. However, it can also be an opportunity for organisations to identify areas for improvement and cost-saving initiatives. By analysing variance, companies can identify underlying factors contributing to excessive material usage and take proactive measures to address them. This data can inform strategic decision-making and process optimization. Additionally, material usage variance is linked to sustainability efforts, as effective management can reduce operational costs and minimise environmental impact by optimising resource consumption. By aligning financial objectives with sustainable practices, companies can lead to more environmentally conscious operations and improve their bottom line.
Formula:
Material Usage Variance = (Actual Quantity × Standard Price) – (Standard Quantity × Standard Price)
Labour Rate Variance:
Labour rate variance is a key metric in standard costing, indicating the difference between actual labour rates paid and expected rates. A positive variance indicates less labour was paid than anticipated, possibly due to efficient employees or favourable wage renegotiations. Conversely, a negative variance suggests more labour was spent than planned, possibly due to overtime costs or wage increases. Understanding labour rate variances helps organisations identify inefficiencies and cost-saving opportunities, enabling proactive measures to improve productivity, negotiate better deals, or optimise workforce allocation. A data-driven approach enhances cost control and fosters continuous improvement.
Formula:
Labor Rate Variance = (Actual Hours × Actual Rate) – (Actual Hours × Standard Rate)
Labor efficiency variance
Labour efficiency variance is a crucial metric in standard costing, indicating a company’s workforce performance. It measures the difference between actual hours worked and the standard hours allowed for output. A positive variance indicates less time spent on production, while a negative variance suggests inefficiency. Understanding labour efficiency variance helps managers identify areas for improvement and cost reduction, optimise production processes, and gauge workforce management strategies’ effectiveness. Monitoring labour efficiency variances is essential for organisations to maintain cost-effective operations and achieve greater profitability. By using this metric, businesses can make informed decisions to drive continuous improvement within their operations.
Formula:
Labor Efficiency Variance = (Actual Hours × Standard Rate) – (Standard Hours × Standard Rate)
Variable Overhead Variance:
One important part of standard costing is variable overhead variance, which shows the difference between what costs actually were and what costs were supposed to be. A new method uses variance as a tool for ongoing growth instead of the old way of looking for differences. By looking at the reasons behind differences, businesses can find inefficient operations, make smart choices, and cut costs. Companies can respond to changes in the market and adjust their cost structures this way, which leads to better financial success and a mindset of always getting better.
Formula:
Variable Overhead Variance = (Actual Hours × Variable Overhead Rate) – (Actual Hours × Standard Variable Overhead Rate)
Fixed Overhead Variance:
Fixed overhead variance is a crucial aspect of standard pricing that can significantly impact overall performance. Understanding this variance requires a deeper understanding of how fixed overhead costs are allocated and absorbed in production processes. By analysing the root causes of the variance, businesses can identify inefficiencies and make informed decisions to improve cost control. A favourable variance may indicate underutilization of resources, while an unfavourable variance may suggest overcapacity or inefficiency. Analysing the timing of certain fixed overhead costs can reveal opportunities for better resource management and cost-reduction strategies.
Analyzing Variances
Examining the variations between actual costs incurred over a period and the standard costs that were anticipated or planned is the process of analysing variances in standard costing. Through this procedure, management is better able to comprehend the causes of these variations and take the necessary steps to reduce expenses and boost output.
- Identify variances by comparing actual costs with standard costs for different cost components such as materials, labour, and overhead.
- Classify variances as favourable or unfavourable based on whether actual costs are lower or higher than standard costs.
- Investigate the reasons behind significant variances to determine their root causes. Factors such as changes in market conditions, production inefficiencies, or material price fluctuations may contribute to variances.
- Develop and implement corrective actions to address unfavourable variances and capitalise on favourable variances. This may involve adjusting production processes, renegotiating supplier contracts, or improving workforce efficiency.
- Continuously monitor variances and performance metrics to ensure that corrective actions are effective and sustainable. Regular review of variances helps management track progress towards meeting cost targets and identify emerging issues promptly.
- Communicate variance analysis findings to relevant stakeholders, such as management, department heads, and budget owners. Timely and accurate reporting facilitates informed decision-making and promotes accountability.
Using Standard Costing in Decision Making
For businesses to make educated choices regarding pricing, cost management, and resource allocation, standard costing is an essential tool. It establishes predetermined costs for materials, labour, and overhead, allowing businesses to compare these to actual costs and identify variances. This information helps managers identify inefficiencies and areas for improvement, leading to proactive decision-making. Standard costing also serves as a benchmark for performance evaluation, assessing production efficiency, and resource utilization. By analysing discrepancies between standard and actual costs, managers can identify potential cost overruns or underutilization, prompting corrective actions. Standard costing also helps determine product profitability by setting competitive prices and ensuring profit margins.